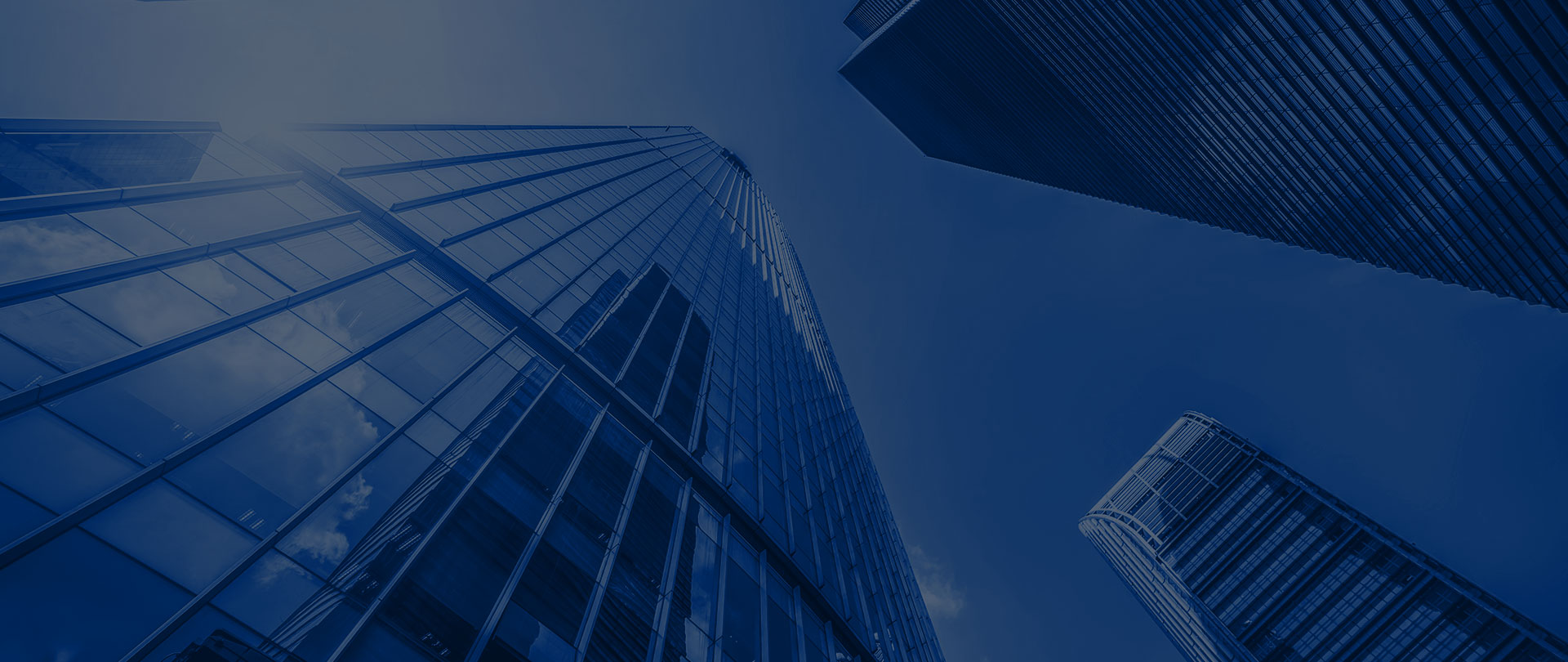
The page you were looking for appears to have been moved,
deleted or does not exist.You could go back to where you were
or head straight to our homepage
5s
The page you were looking for appears to have been moved,
deleted or does not exist.You could go back to where you were
or head straight to our homepage
5s
The page you were looking for appears
to have been moved,deleted or does not exist.
You could go back to where you were
or head straight to our homepage
>5s